This series of weather-related blogs has touched on heat, rain and wind. Now it is time to put the challenges of cold under the magnifying glass and see how they can turn railway reliability upside down.
Snow
When we think of cold weather we often think of snow. This fluffy white stuff can challenge the railway in several ways.
Drifting snow
Snow may look pretty and idyllic, but it provides a real risk to railways, particularly when wind causes it to drift and block the safe passage of rail traffic. Whilst it may look fluffy and light when it falls, its weight soon builds up into a substantial obstacle to passing traffic. A variety of both rolling stock and infrastructure technologies are used to keep routes clear including snow ploughs, snow blowers and snow fences the last of which aim to keep snow accumulations away from the tracks rather than over them.
Avalanche
In hilly or mountainous regions snow accumulation above the railway route can pose a real rail risk from avalanches. Two risk scenarios are often considered. The first is blocking of the tracks caused by an avalanche which a train then runs into. Whilst snow may seem soft and harmless when we are playing with it, when a train runs into several hundred, or even thousands of tonnes of snow blocking the track, the derailment and accident risks are very real. The second scenario is an avalanche occurring as the train passes, striking the train sideways with a wall of snow as it attempts to pass. This perhaps less likely occurrence carries a very real risk of sweeping the train from the tracks and down the slope burying the crash debris at the same time.
In avalanche prone areas infrastructure such as snow/avalanche shelters can be built over routes to protect in vulnerable areas. Avalanches can also be started deliberately to limit their size and avoid them hitting passing traffic. These are often started using explosives placed, dropped, or fired into the slope at risk.
There are various methods to remotely detect an avalanche including tilt sensors, fence mounted wires/cables which are all disrupted by the moving snow, but these also come with the drawback that they need to be reset after activation. Whilst LiDAR and CCTV can also be utilised to monitor for a clear route at local levels, their effectiveness in heavy snowfall can be limited as they rely on visual information which can be lost in heavy snowfall.
Distributed Acoustic Sensing is also a potential way to monitor significant avalanche events due to the ground vibrations they cause in a similar way to detecting landslides. Whilst not yet a commercial product offering from Sensonic, if this is something of interest then get in touch.
Ice / Cold
This slippery issue arrives as temperatures fall and water moves from a flowing to a solid problem.
Tunnels
Water ingress into tunnels combined with freezing temperatures can generate some pretty impressive Icicles/ice formations. Whilst undoubtedly pretty, a train running into potentially several tonnes of solid objects impacting the driver is not a hazard to be ignored. Removing this hazard from height also requires care and track electrified with overhead catenary can further complicate this challenge.
The permanent fix is to prevent water ingress into the tunnel, however that is often easier said than done. In the short term, good weather forecasting and asset knowledge is key to identifying where this risk may occur and then putting into place suitable adverse weather plans to manage the risks.
Icicles hanging from a tunnel roof. Image from Network Rail.
Rollingstock
Ice may build up on and beneath vehicles. This can lead to malfunctions such as doors not opening and closing properly on passenger vehicles, or ironically overheating as radiators become blocked with snow and ice.
Snow and ice can also build up into large solid chunks weighing hundreds of kilos or more, which then cause hazards to other vehicles and infrastructure should they fall off. Substantial ice formation can also impact the safe working of critical systems including brakes. De-icing of trains in such situations can take significant time and resources as it does aircraft at airports.
Vehicle design changes can help avoid ice build-up using rubber flexible parts to prevent large accumulations, but these typically need to be specified at the design stage for rollingstock that is expected to experience these issues regularly.
Speed limits may also be introduced for high-speed trains to prevent the greater air turbulence from dislodging large blocks of ice into the path of an oncoming train which can double the impact speed of falling ice.
Ice build-up on the braking system of a passenger train. Image from Liljewalch, CC BY-SA 4.0
Overhead wiring
On railways with overhead electrical power supplies ice build-up on the wires causes two main issues. The first is the additional weight of ice which can build up to substantial levels causing wires to sag or even in extreme cases their supporting structures to collapse due to overload.
Ice build up has caused the overhead catenary powerlines to collapse. Image from the Railway Transport Union of Slovenia
The second is the effect on the electrical transmission between the contact wire and the pantograph of the vehicle. Due to gravity most ice tends to form on the bottom of the wire exactly where the pantograph contacts slides. The formation of ice here poses both a mechanical risk as the carbon pantograph can hit icicles and ice accumulations at speed, as well as an electrical risk. Ice is not a good conductor of electricity and so in extreme situations the pantograph can lose electrical contact with the line causing the train to lose power. More commonly electrical arcing between the pantograph and wire greatly increases causing accelerated wear to both the pantograph and wire as well as reduced power transmission capability.
Electrical arcing between catenary contact wire and pantograph due to ice formation on the wires
Various methods are used to reduce the ice build up to acceptable levels, from running extra empty vehicles sometimes known as ‘ice-breakers’ to mechanically knocking ice build-up from the wires, and even using controlled short circuits to heat the wires to melt the ice from their surface. Research work has even been done to apply de-icing fluids to the wires to prevent excessive ice build-up. The same ice challenges can apply to 3rd and 4th rail electrification too although some systems are better shielded from the weather than others.
Removing ice from overhead wires after an ice storm in China
Switches and Crossings
A key part of route performance is the switches and crossings' reliability, allowing trains to change tracks to reach their desired destination. Should these become blocked with snow or ice, then trains are not allowed to pass, crippling network performance. As they are such a critical part of reliable performance then despite their outdoor nature, they are often heated to prevent snow and ice buildup. Modern systems tend to use electrical heating strips attached to the rails; however, some older systems still use open flames from gas or other fuels to keep the switches and crossings above freezing point which are quite striking sight!
Rail heating using gas burners in the United States
Other solutions include applying antifreeze solutions directly at the site or handheld heating with torches.
Whilst monitoring of electrical currents and gas flows can be used as an indicator of whether these heating systems are working, overhead inspection via helicopter or drone using thermal cameras is often an easy way to identify any defective areas of heating quickly and without needing people to directly access the site.
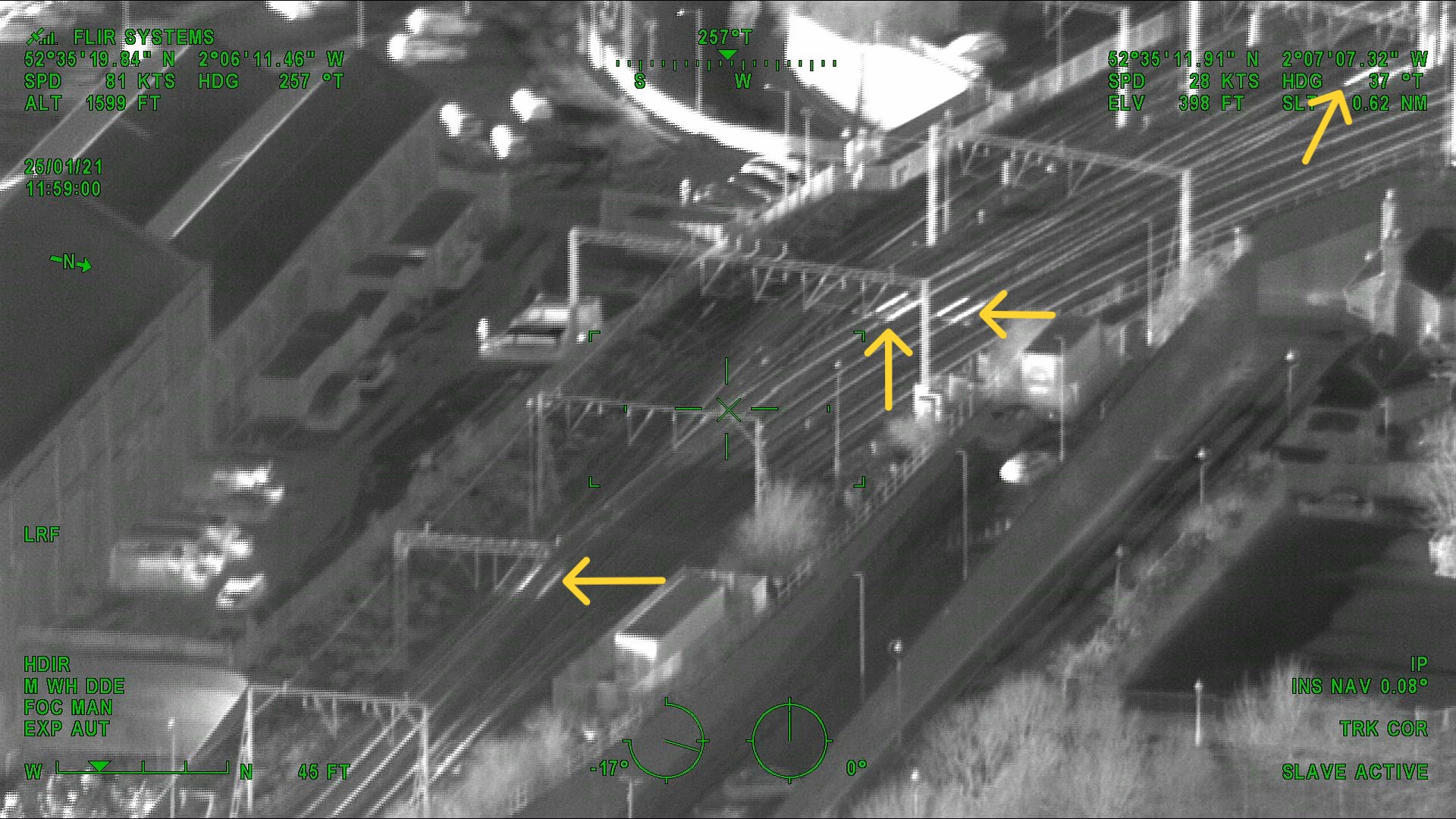
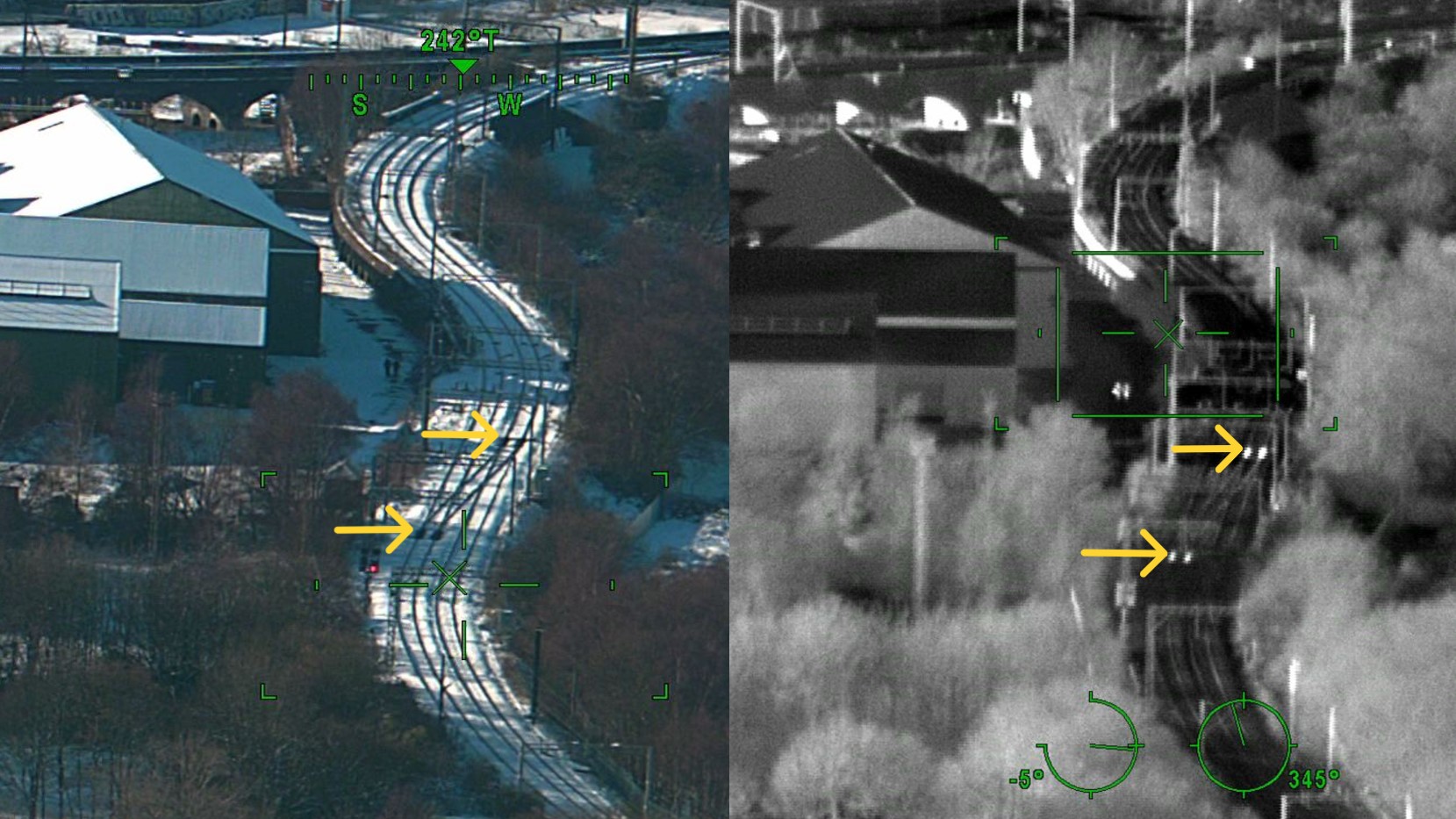
Thermal views from Network Rail showing switch heating inspection - Arrows indicate location of rail heating
Broken Rails
Modern rail tracks are usually constructed from continuously welded rail. Due to the long-welded rail lengths, these rails are stretched during installation so they can cope with thermal expansion in the hotter seasons of the year (to avoid them buckling / sun kinks). However, as temperatures fall, so too does the natural rail length. A 1km rail shrinks by over 11cm per 10°C temp fall. (or 4 inches per mile per 10°F if you prefer). However, as we design track not to move, this means that the stretch force in the rails increases as the rails get colder, (as their length remains pinned in place by the ties and ballast). Should there be a defect in the rail, or the stretch forces become too large then the rail itself can break under the stress, called a pull-apart in some regions. As the stress in the rail is released a gap then forms between the rail ends. A broken rail is never good, one with a gap next to it is worse still.
A broken rail / weld. Note the gap that forms due to the rail stretch being released. Image from B.A., CC BY-SA 3.0
Broken rails are typically identified by periodic visual inspection, by a report from train personnel, or where track circuit signalling is used a rail break typically produces a track circuit failure which then sets the signals to stop over the affected track as soon as it occurs. There are also other techniques to identify broken rails and we’ve had good success identifying and locating them with our Distributed Acoustic Sensing equipment as part of our track condition monitoring application. This works by detecting the greatly increased vibration as trains cross the gap between the broken ends of the rail as we are looking for changes in asset vibration behaviour over time. It must be noted that not all broken rails leave a gap in the running surface, but 'pull apart' failures do. If this is something of interest, then get in touch.
Frozen ground
Should temperatures plummet for extended periods then frozen ballast and/or ground heave may become significant issues for a railway. Waterlogged ballast when frozen loses its natural resilience becoming very stiff causing localised hard spots along the route. Sudden changes in track stiffness are bad for both ride quality and asset life. If large areas are affected the expansion of water as it freezes can also cause the entire track bed to move or deform as water expands as it freezes. Both effects can lead to track alignment faults affecting the safety of the track and are not something easily resolved as infrastructure changes may be required. Detection of such faults is usually done from train crew reports or periodic inspections by inspectors and geometry recording vehicles.
Summary
Whilst many media headlines surrounding climate change focus on global temperature increases, this perhaps understates the effects of climate change we experience, as weather patterns shift making some areas hotter and indeed some colder. The effect of global temperature increase serves to increase the energy that our weather systems contain, whether that be wind, rain, or snow as well as global temperatures when the sun does shine.
We all need to be prepared to adapt to climate change, whatever the cause we must adapt to survive as both industry and species. Let's not let climate change turn our world upside down.
This series of articles has touched on some of the challenges that climate change and increasingly extreme weather poses for the railway and some of the ways it can rise to these challenges. If you’ve missed any of them, you can find links here:
Like this article? Then share it with the button at the top.